Delivery vehicles are an asset to every operation. Besides ensuring that the vehicles are maintained in good working order, operators can utilize technology like GPS systems to gain fuel savings and even deter internal theft.
In talking to operators I’ve made an informal list of the top five challenges that operators face related to their fleet and how a GPS has worked to help.
1. Decreasing speeds
For many trucks and large delivery vehicles, fuel efficiency decreases as highway driving speed increases. That is why many operators will use systems that limit the top speed of their delivery vehicles to 55 miles per hour or even 65. I’ve seen statistics that 75 miles per hour uses nearly 30 percent more fuel than 65. GPS systems can monitor speeds, which helps operators enforce their highway driving rules.
2. Less time idling
Idling is a tremendous fuel waster. GPS systems can monitor when a truck is on, but not moving, as well as the speed it travels. In fact, many systems can even send alerts to management when a certain amount of idling time has been reached, so the operator can find out the cause. Perhaps the idling is due to something outside the driver’s control, such as an accident or road construction. Other deliveries or technicians to that area could be rerouted to avoid late service. On the flip side, notifications of idling hangs out in a certain location in order to extend his or her hours worked. With data from the GPS, the manager can address and correct this behavior.
3. Coordinating extra trips
Long time operators know that reacting to changing service needs is an important part of the daily vending operation. Bill validators jam, coffee vending machines get clogged, cashless readers go down, etc. There are any number of issues that arise on a daily basis that require extra trips out to a location. Knowing which driver or technician is closest to problem equipment can be an effective and cost efficient way to handle these daily extras. Because a GPS system constantly monitors the location of each vehicle, it is an excellent way to determine which staff member is closest. This can really increase customer support, ensuring that quick response customers are looking for. And it saves on fuel economy, trips and possibly even staffing.
4. Deterring theft
While most people are honest, there are always temptations. Route drivers, service techs and all staff are more likely to keep following rules and doing the right thing if they know the operator is watching. Perhaps a manager compliments them on staying within the speed limits and still getting done with their route early. Maybe it’s reminding them not to stop off home between stops. Once the drivers know you’re watching them, they are less tempted to do what they are not supposed to do.
5. Avoid pitfalls
For drivers that don’t have a dedicated route and instead use dynamic scheduling, unforeseen heavy traffic can stall the timely service your company prides itself on. Drivers of regular, dedicated routes, likely know what areas to avoid, but can always get stopped by an accident. Avoiding these money wasting areas is important. Operators have used GPS systems that regularly receive real-time traffic updates to save them from these last minute service headaches.
Identifying a challenge is the first step to overcoming it. That is how looking at your vehicles, the speeds, idle times and actual travel areas will save your vending operation money. The benefits you receive will apply regardless of the GPS system you consider. For the right size operation willing to invest in such a tool, the savings can make it a good investment.
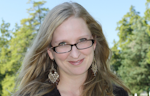
Emily Refermat | Editor
Emily has been living and breathing the vending industry since 2006 and became Editor in 2012. Usually Emily tries the new salted snack in the vending machine, unless she’s on deadline – then it’s a Snickers.
Feel free to reach Emily via email here or follow her on Twitter @VMW_Refermat.